The benefits of single fibre testing on sheep wool
Wool fibres have been used to produce textiles throughout much of human history. Typically curled, fine fibres, wool is commonly sourced from sheep and goats, as well as other mammals. Today, sheep’s wool is the most commercially important animal fibre used in the textile industry, from fashion to functional clothing, and interior textile products such as carpets. There is also a significant increase in diverse uses for wool technical textiles and non-woven applications such as bio-composites and insulation.
The increasingly diverse applications for wool fibres follow the trend seen for other natural fibres. As non-textile materials focus more on natural fibres, the study of the mechanical characteristics in new and novel applications becomes more important. In this article we aim to highlight the benefits and capabilities of single fibre measurements using samples of raw wool fibres taken from British sheep breeds of Cotswold, Welsh Black, Norfolk Horn, Southdown and Ryeland in an internal study conducted in our UK Applications Laboratory.
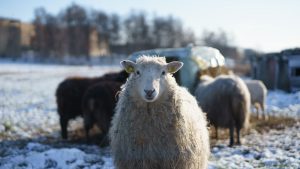
Dimensional Measurements
Wool fibres are typically not circular and like most natural fibres, vary in diameter, both between fibres and along the length of the individual fibres. The Dia-Stron Fibre Dimensional Analysis System FDAS770 utilises a Laser Scanning Micrometer to conduct accurate, non-contact dimensional measurements of fibres. The fully automated fibre rotation and translation allows for multiple measurements along the length and with full 360° rotation, making it ideal for obtaining dimensional information for fibres such as wool.
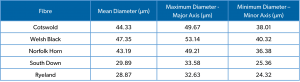
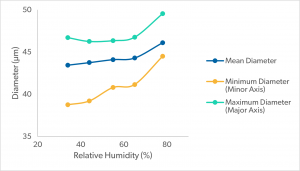
Single Fibre Tensile Strength
The tensile properties of wool can be measured on single fibres, bundles and staples, providing key information about the Young’s modulus and material strength. This is commonly achieved by measuring the force to break under constant elongation. Strength measurements for wool are often measured on staples or bundles, but single fibre testing is regarded as a more exact measurement of strength (1). The single fibre mechanical properties of wool have been fundamental in the understanding of other alpha-keratin based fibres, and have served as a foundation in developing new fibres (2).
Single fibre measurements have traditionally been seen as challenging, especially when using manual tensile testing systems. However, the use of automation and appropriate sample mounting overcomes these challenges, providing higher throughput and larger data sets with significantly improved reproducibility. This facilitates statistical modelling that can distinguish subtle, yet key variations in sample type or treatment. Dia-Stron’s unique brass crimp or plastic tab mounting systems are designed to hold fibres securely without damaging the fibres prior to the tensile test. The samples can then be automatically transported between various testing modules without user interaction, reducing errors and pre-damage of the fibre, as well as freeing up the user to work on other activities. Controlling the environmental conditions is also an important factor when measuring the strength of natural fibres. Dia-Stron’s automated single fibre systems fit entirely within an environmental chamber, enabling measurements at fixed humidities and temperatures as specified in standards such as ASTM D1776/D1776M-20 (3).
During this study, 50 individual fibres were selected from each of the wool staples and the dimensional and tensile parameters were measured using the Dia-Stron FDAS770 and LEX820 linear extensometer respectively. The extension and force to break were recorded. To compare the load-extension behaviour between the different individual fibres, the direct effect of their dimensions was removed. The cross-sectional area of the fibres calculated from the FDAS770 measurement was then used to convert the load to stress. If the linear density is known, these values can also be inputted into the Dia-Stron UvWin software and the specific stress or tenacity in cN/tex can be calculated.
Variability in fibre strength is caused by the inherent flaw distribution along a fibre (4) and by the fibre-to-fibre strength inconsistency within a batch of fibres. In wool, these effects occur due to variations in natural growth, environmental damage and through processing methods. To analyse the statistical distribution of fibre strength of the different sheep breeds in this study, a 2-parameter Weibull distribution (figure 2) was fitted to the fibre break stress data to obtain the shape and scale parameters. The shape parameter describes the variability in the strength, with a higher value suggesting lower variability. The results in this study imply that fibres from sheep breeds with smaller diameters (e.g. Ryeland and Southdown) exhibit a lower stress to break and an increased variability in strength compared to sheep breeds with thicker fibres.
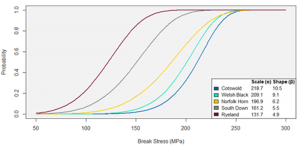
Fibre Fatigue
Wool fibres typically undergo numerous mechanical processes between their source and the finished product. Repeated tensioning, flexing, and bending commonly occur during fibre processing and end-use applications, which can cause fibre fatigue. Fibre failure may occur because the maximum strength in a particular mode of deformation has been exceeded. More commonly, however, fibres fail because they have been subjected to cumulative application of relatively low stresses, which are well within the elastic limit. These repeated stresses build up, originating at microscopic cracks and flaws, propagating within the fibre substructures and eventually leading to breakage.
Accelerated fibre fatigue can be simulated in the laboratory using Dia-Stron’s CYC802 cyclic fatigue system, where single fibres can be subjected to either cyclic tension or buckling-tension fatigue. From such experiments, the number cycles to break are measured, which can be used to understand and predict fibre failure under dynamic conditions.
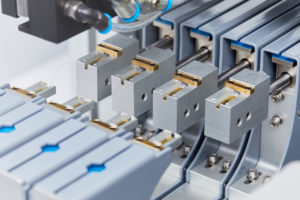
Conclusion
The increase in applications of natural fibres (including well-established fibres such as wool) has led to a renewed interest in fibre mechanical testing, particularly for properties or applications not previously considered in the literature. Natural fibres offer a strong alternative to synthetic fibres, however, testing is vital to understand the inherent variations in the fibre properties, as demonstrated here in the variations between wool from different sheep breeds. The tests carried out for this article have shown the convenience and range of testing available with Dia-Stron’s systems, enabling clear differentiation of fibre properties from different sample sources.
References
1. A. Nechwatal, et al., Developments in the characterization of natural fibres properties and in the use of natural fibres for composites, Compos. Sci. Technol., (2003), 63, 1273-1279
2. J. Müssig, Industrial Applications of Natural Fibres – Structure, Properties and Technical Applications – Wiley Series in Renewable Resources (2010)
3. ASTM D1776/D1776M-20 – Standard Practise for Conditioning and Testing Textiles
4. F. Wang, Modified Weibull Distribution for Analyzing the Tensile Strength of Bambo Fibers, Polymer (2014), 6(12), 3005-3018